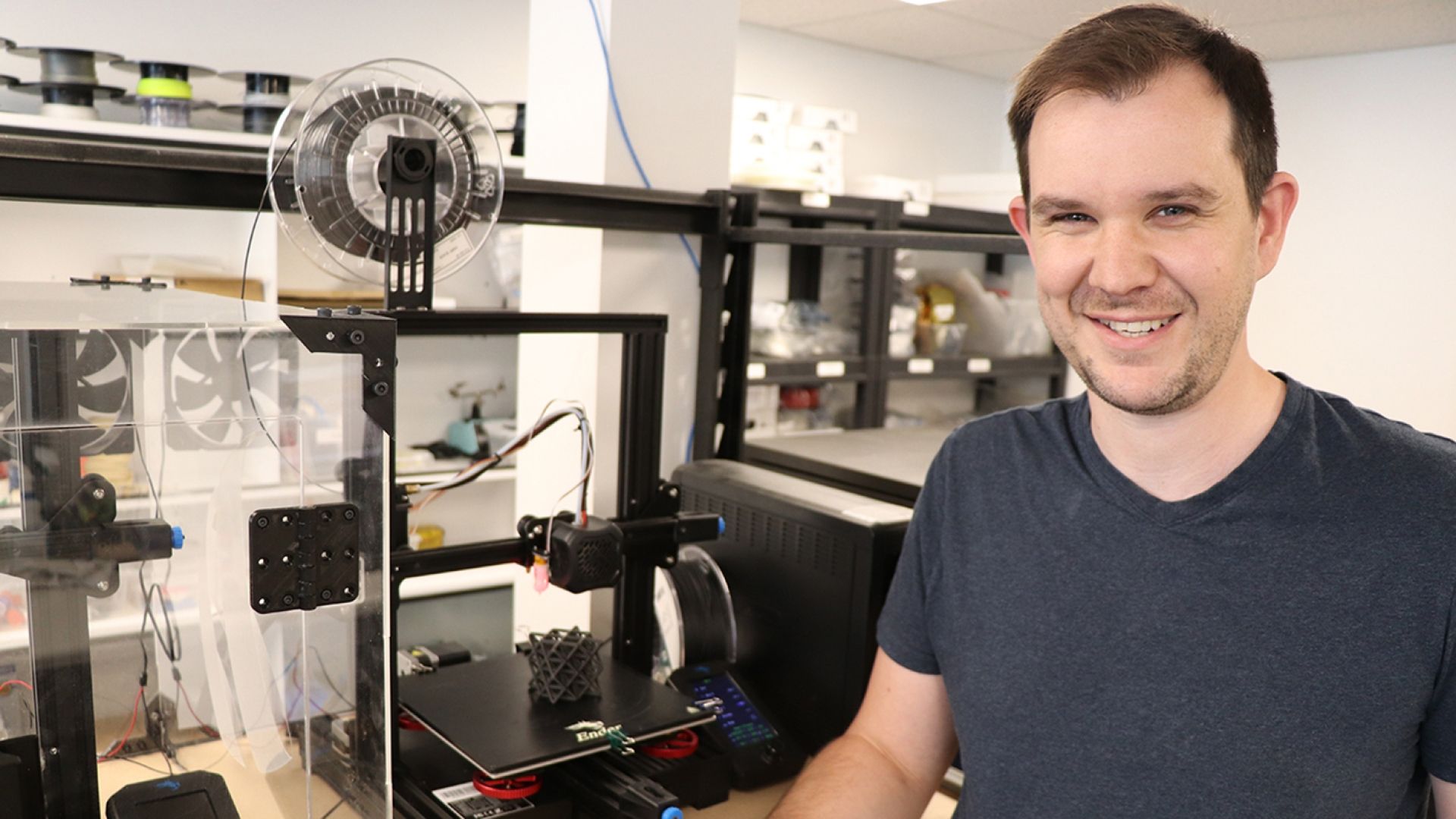
Innovative Technologies
Combining technology with existing or emerging industry is critical to the sustainability of our rural region. Being able to manufacture things locally and quickly is valuable. The incredible Kootenay landscape offers up unique challenges—parts and cutting-edge services can be hard to find.
Our rural region is home to a diverse range of industry partners and businesses—from particle accelerators and natural resource companies to outdoor adventure manufacturers.
Our advanced manufacturing research team is here to support you in developing new products and reverse engineering critical parts by designing and testing new applications of innovative technologies.
The work is accomplished at the Selkirk Technology Access Centre (STAC), one of 60 NSERC-funded Technology Access Centres (TACs) across Canada, and one of three located in British Columbia.
Over $2 Million in Specialized Equipment
We house over $2 million in specialized equipment and cutting-edge technology, including one of rural Canada’s first 3D metal printers, augmented and virtual reality capacity, high-end 3D scanning technology and industrial-scale waterjet and laser cutters. Our equipment—combined with the technical expertise of our highly skilled and passionate staff and students—can support you in developing, advancing and commercializing your products and services.
We provide customized advanced technology training, help you secure funding and provide referrals to regional services.
Research Focus Areas
Large-format 3D printing
Large format 3D printing provides unique opportunities for rural manufacturers and developers to compete in a global market.
It involves specific research in materials development specific to large-format printing—including foam and biodegradable plastics.
At Selkirk Innovates, we are developing key advancements in large-format additive manufacturing, including custom extrusion technologies. The knowledge and processes we develop are transferred to our industrial partners to expand their suite of services, extend their customer base and reduce production costs.
Additive manufacturing has taken the world by storm, although adoption by industry has not progressed as fast in rural areas. The major constraint to this adoption is the limited build volume, limited material options and high cost of industrial grade 3D printing technology. The advancement of large-format additive manufacturing, including customized material extrusion technology, can alleviate this constraint.
Combining additive and subtractive manufacturing
Applied research in combining large-format 3D printing and subtractive manufacturing technologies, with collaboration from multiple industry partners.
We are developing key advancements in both small- and large-format additive manufacturing, including the implementation of custom extrusion technologies and the development of hybrid additive-subtractive manufacturing processes.
The knowledge and processes developed during this project will be transferred to our industry partners to expand their suite of services and customer base. The addition of hybrid additive-subtractive manufacturing capabilities to our industry partners’ diverse production methods will greatly enhance their product offerings while reducing production costs by saving time and dramatically reducing waste.
By-product utilization
Utilizing by-products from the mining and forestry industries in advanced manufacturing.
Applied research in recycling plastics for large-format 3D printing and other manufacturing processes.
Transfer of designs, prototypes and knowledge gained goes directly to contributing industry partners.
Developing engineering-grade biodegradable plastics
Advanced BioCarbon 3D, a Rossland-based company, is en route to producing high quality, engineering grade plastics made from wood by-products. The result will be a truly biodegradable product that could revolutionize and clean up the plastics industry through its diverse applications, while simultaneously providing the forest industry with a market for waste wood.
Researchers at Selkirk Innovates are lending a hand through materials testing and optimization of the company’s manufacturing process.
This project was featured on 3dprintingindustry.com.
Rapid prototyping
Rapid prototyping using advanced manufacturing provides a unique opportunity for industry, students and researchers to build and share knowledge.
We are passionate about growing our industry relationships through small, rapid turn-around applied research and fee-for-service projects. We conduct a wide variety of projects using rapid prototyping, reverse engineering, digital fabrication, robotic automation and advanced manufacturing technologies. Students are given the opportunity to work directly with industry partners to solve real-world challenges, and they are provided with unique access to state-of-the-art equipment, technologies and training from faculty with highly specialized expertise.
Research Spotlight
3D Terrain Model for Ekati Diamond Mine
The Independent Environmental Monitoring Agency (IEMA), which oversees the Ekati Diamond Mine in Canada’s Northwest Territories, was looking for an effective way to show indigenous and other local communities what the mine site would look like in the future after closure.
Selkirk Technology Access Centre (STAC) provided an interactive portable map application, showcasing the current and future status of the mine. For consultation purposes, STAC built a 3D terrain model of the entire site—which is over 40 kilometres wide—and used a data projector to project imagery, like a caribou migration path, onto the model. This made it more interactive to help facilitate the discussion with people impacted by the mine.
Custom 3D-Printed Parts for UV Water Treatment System
Selkirk Technology Access Centre (STAC) worked with 9dot Engineering and Aqua Diversities Waterworks in Nelson, BC, to provide a critical plastic fitting for the UV water treatment system that was damaged due to the heat and UV in the system, and the parts were discontinued.
The small rural village these companies were serving would be looking at a very large unplanned capital expense during COVID-19. STAC came to the rescue and 3D-scanned and reverse-engineered the part and then 3D-printed test pieces to ensure proper fit before it was machined. The prototypes fit but were brittle. One of STAC’s researchers (a millwright machinist) reviewed and further improved the design by using a UV-resistant plastic that was precisely CNC-machined. This part was strong and functional. The client was able to use the files they own to work with another local machine shop for larger orders.